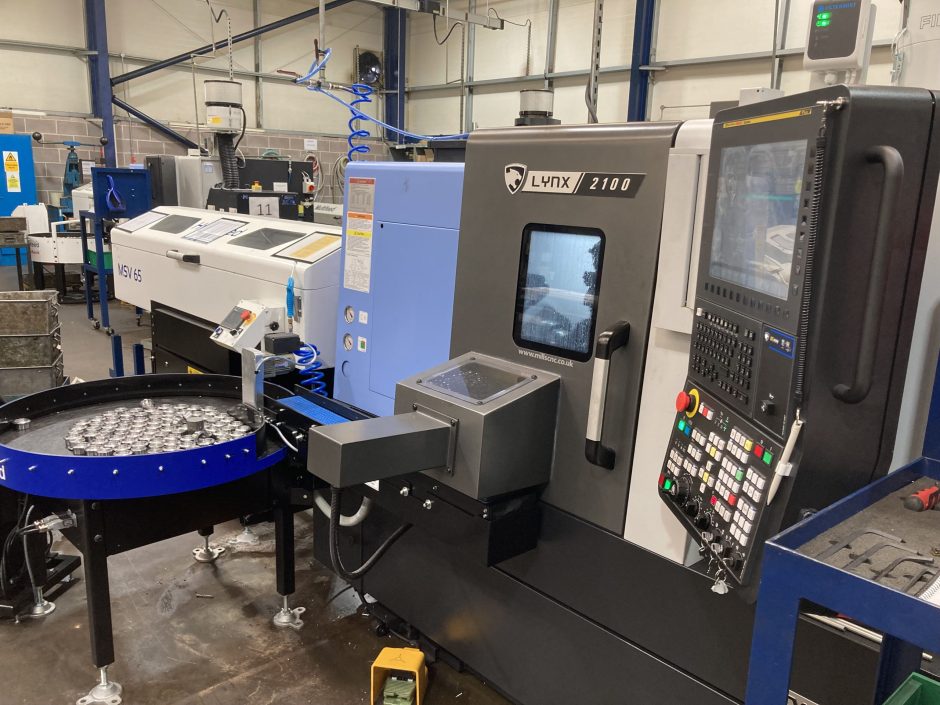
Market-leading ball transfer unit (BTU) design and manufacturing specialist Alwayse Engineering invests in a new DN Solutions’ high-performance two-axis lathe from Mills CNC to meet the anticipated high demand for its re-designed and ‘soon-to-be-launched’ series of 805 heavy-duty ball transfer units – a proven, reliable and industry-specified air cargo materials handling solution.
Mills CNC, the exclusive distributor of DN Solutions’ and Zayer machine tools in the UK and Ireland, has recently supplied Alwayse Engineering Ltd., a leading, globally-recognised ball transfer unit design and manufacturing specialist, with a new DN Solutions’ two-axis lathe.
The machine, a Fanuc-controlled 8” chuck/65mm bar diameter Lynx 2100B lathe, was installed at Alwayse Engineering’s large, impressive and integrated manufacturing facility in Birmingham in March 2025.
As part of the investment package, the machine was supplied with a HydraFeed MSV65 servo-driven, short magazine bar feeder, to facilitate continuous, unattended production, and a HydraFeed ROTA-RACK parts accumulator and handling system with an integrated belt conveyor, for improved machined part storage and protection.
Since being installed, the new Lynx 2100B has been put through its paces machining the new single-piece, carbon steel bodies for the company’s re-designed and ‘soon-to-be launched’ 805 series of low-profile, high-load capacity and heavy-duty ball transfer units, used primarily, in air cargo movement applications.
805 unit bodies are processed from solid mild steel bar stock. They are characterised by their tight, tied up tolerances and exacting surface finish requirements. (Ensuring consistent high part quality and repeatability are critical machining factors.)
805 ball transfer unit steel bodies are 62mm in diameter and 34.5mm in length and are machined in one set up on the Lynx 2100B. Machining operations include (front end) rough and finish boring of the bodies’ interiors to produce the desired internal ‘hemisphere-shape’, and (back end) burr-free, parting-off operations to cut off the machined parts from the remaining bar stock.
Part cycle times are short (approximately 80 seconds) and, once machined on the Lynx 2100B, the bodies are finish machined on one of the company’s other Lynx lathes where a series of multi-dirt exit holes (that prevent debris build-up and enable more efficient maintenance and cleaning) are machined on the bottom of every unit.
Following case hardening and zinc-plating operations, the units are then assembled where a number of small diameter stainless steel balls and a larger diameter stainless steel or carbon chrome load ball (30mm or 45mm in diameter) are inserted to each unit’s interior before being sealed with a retaining (stamped) outer metal ring.
805 ball transfer units are classified as ‘core line’ products by Alwayse Engineering, which means that they are held in stock and are always available – ready to be supplied to customers quickly and efficiently.
Alwayse work closely with their customers to design highly-customised and modular ball transfer decks which comprise a series of 805 ball transfer units spaced in a grid pattern and mounted into steel top plates that are attached to strong and stable steel-fabricated sections or frames.
The shape of these sections, and the number of ball transfer units used, depend on the specifics of each application (i.e., size of aircraft cargo decks and the ULDs (Unit Load Devices) used, the warehouse floor space available etc.), as well as the type (load and size) of goods being moved and transported (e.g. cargo, mail, baggage etc).
Alwayse Engineering can provide customers with complete ball transfer decks, where required and, within its Birmingham facility, has its own in-house fabrication operation to manufacture the top plates and sections.
As well as complete turnkey solutions, Alwayse Engineering supplies the ball transfer units to integrators and resellers who design the units into the final application, they also support with design services.
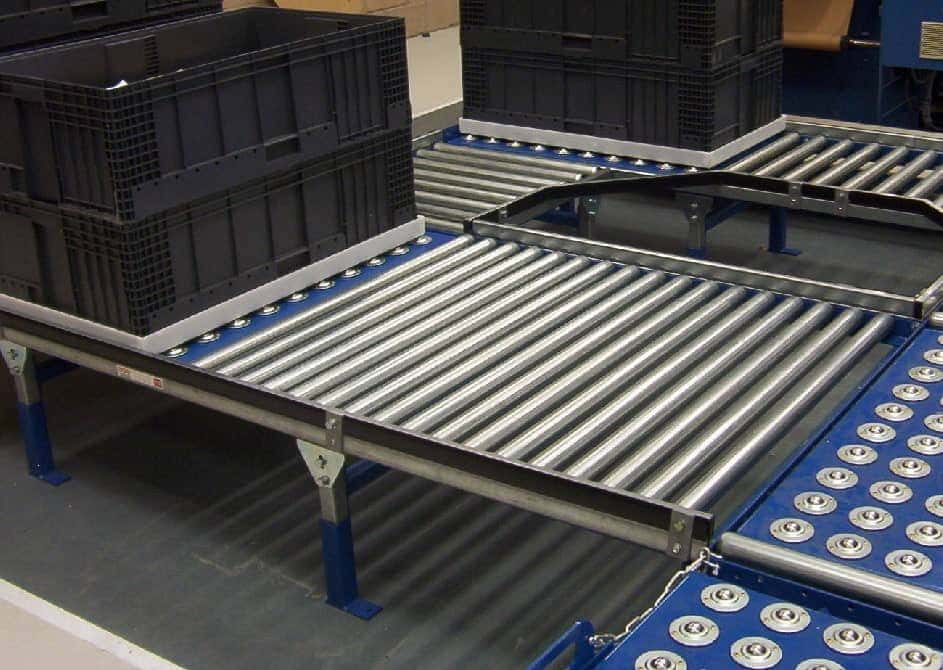
805 Ball Transfer Units – development
Alwayse 805 Air Cargo ball transfer units are recognised, internationally, for their reliability and durability, and are used extensively within tough and demanding materials handling environments (e.g.., air cargo and freight movement).
The company first introduced its precision machined 805 series of heavy-duty ball transfer units into the market back in the late 1990s and, with IATA (International Air Transport Association) recognition, rapidly became accepted as the industry standard.
Recent and successful Alwayse 805 ball transfer unit and ball transfer deck installations include those at Bogota Airport, Columbia and at Heathrow Airport (Terminal 5), London.
Committed to continuous improvement and innovation, the company, back in 2023, following extensive research and customer (distributor and end user) feedback, embarked on a major ‘root and branch’ product redesign and redevelopment programme.
The programme coincided with the company being taken over in March 2023 by Lifco, a Swedish-based investment company specialising in the acquisition and development of market-leading niche businesses.
With prototyping and pre-production development and testing completed, the company is now in full production mode – ready to launch its new 805 series of ball transfer units into the market.
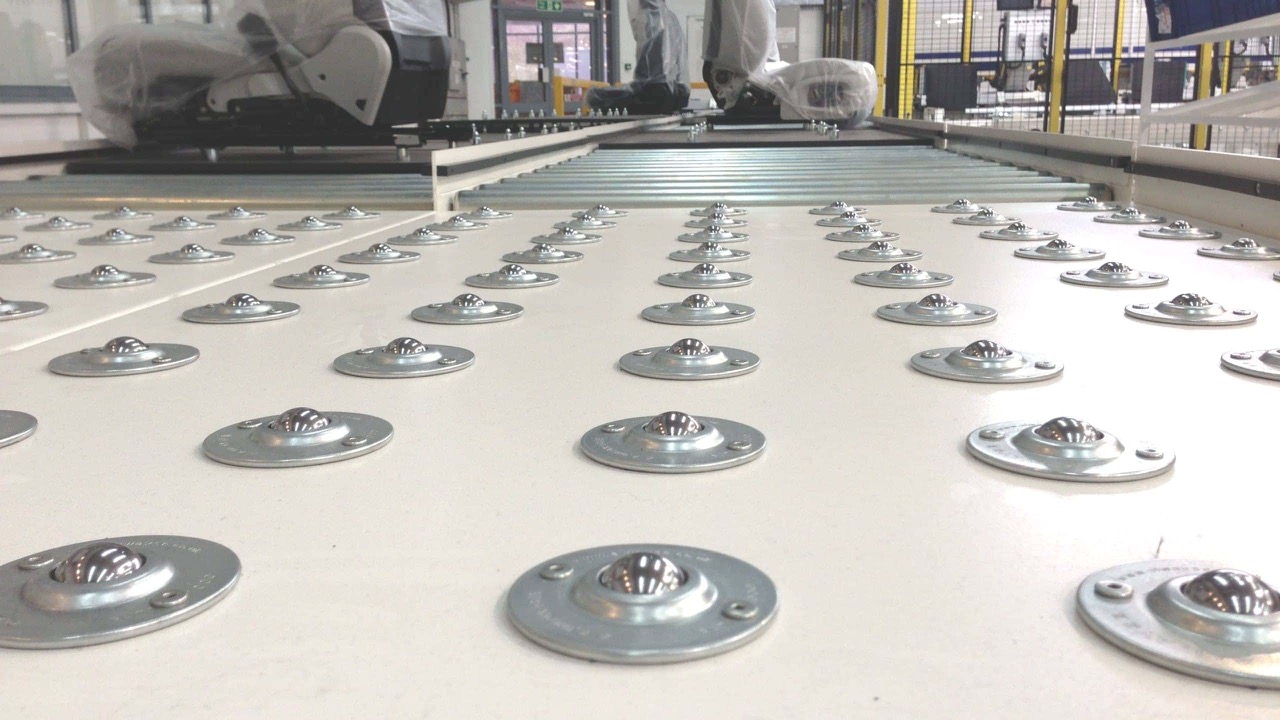
New 805 ball transfer units – advantages
Alwayse’s new 805 ball transfer units are built to last and can operate, with no reduction in performance, in both wet and dry conditions.
Like their predecessors, the new 805 units ensure smooth cargo movement with minimal resistance, but the newly designed units have specific advantages and strengths over their earlier counterparts i.e., they are quieter (noise reduction down to 64dB) and lighter.
Alwayse Engineering and Mills CNC
Alwayse Engineering is no stranger to DN Solutions’ (previously Doosan) machine tools, and its relationship with Mills CNC started back in 2006.
The new Lynx 2100B installed in the company’s well-resourced machine shop has been positioned adjacent to five older DN Solutions’ and Doosan compact Lynx lathes acquired by Alwayse Engineering over the last 19 years. These machines comprise 2 x Lynx 220LC, 1 x Lynx 220C, 1 x Lynx 2100LMSB and 1 x Lynx 2100A.
“DN Solutions’ and Doosan machines are proven performers and have significantly improved our in-house machining capacity and capabilities.
“Our Lynx lathes deliver the accuracies and repeatability’s, the fast processing speeds and the machining flexibility we need to increase our productivity (i.e., reduced set up and cycle times) and improve our process efficiencies.
“Over the years we have developed a good working relationship with Mills CNC. In addition to providing us with best-in-class machine tool technologies, we can also vouch for the efficacy of the company’s delivery and installation operations, its CNC training provision and its after-sales service and support too.”
Richard Cutler, Engineering Manager at Alwayse Engineering
Unsurprisingly, when the company was looking to invest in a new lathe dedicated to the manufacture of its newly-designed 805 ball transfer units – Mills CNC was one of three machine tool suppliers Alwayse Engineering approached.
“Mills provided us with a competitive quote for the new compact lathe. Our knowledge of, and previous positive experience with, DN Solutions’ Lynx lathes combined with our established relationships with Mills CNC put them in the driving seat and resulted in us placing the order with them.”
Richard Cutler, Engineering Manager at Alwayse Engineering
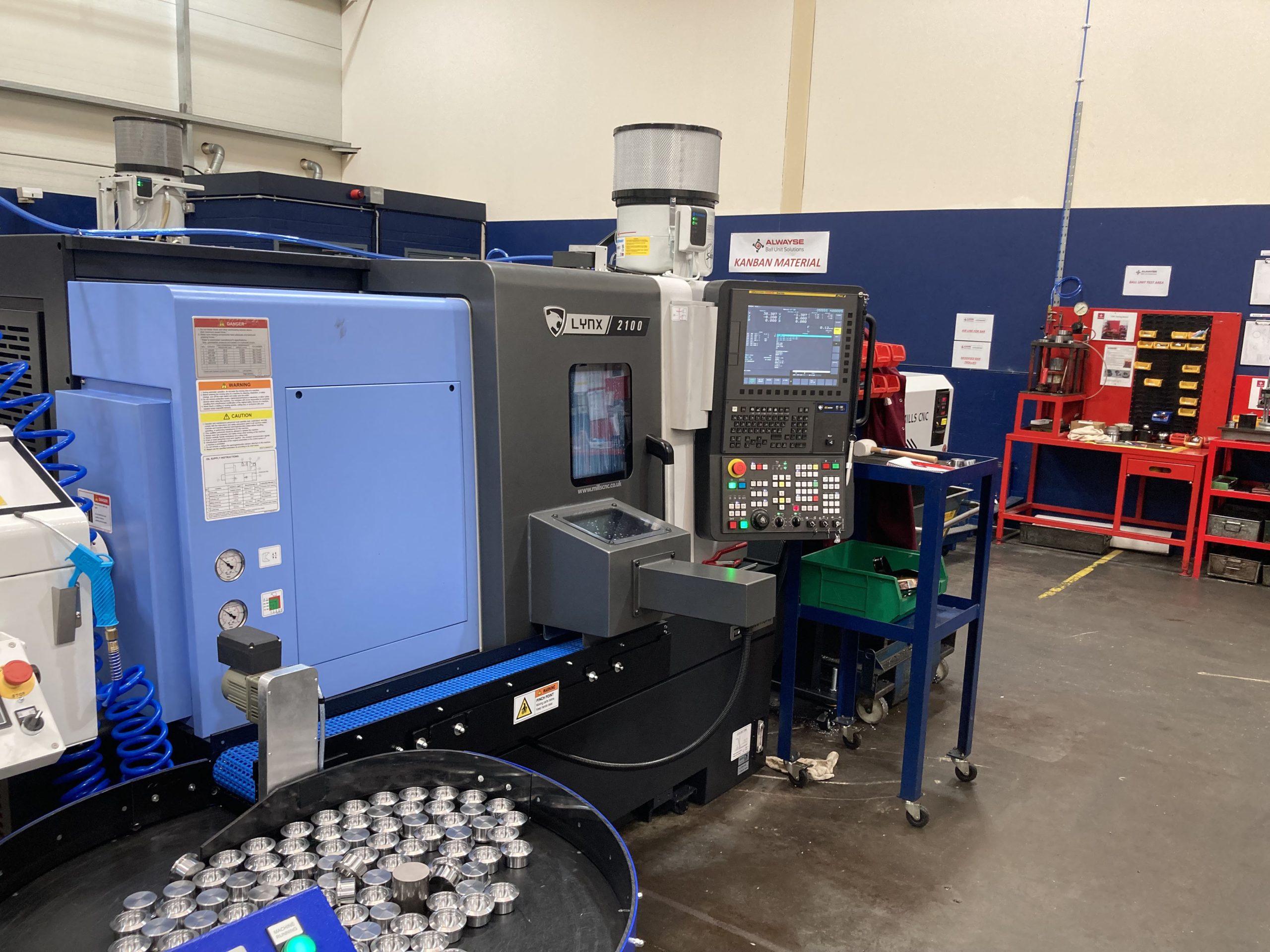
The Lynx 2100B – a closer look
DN Solutions’ Lynx 2100B is a popular, best-selling compact lathe equipped with a 15kW/4500rpm spindle and a 12-station, servo-driven turret with fast tool change capabilities.
The machine boasts 30m/min rapids on its X-axis and 36m/min rapids on its Z-axis, and features a 350mm maximum turning diameter and a 330mm maximum turning length.
In addition to the HydraFeed bar feeder and ROTA-RACK parts accumulator, the machine supplied to Alwayse Engineering was also equipped with the Doosan Fanuc iPlus control with 15” touchscreen iHMI, a FilterMist extraction unit and a customised pneumatic arm integrated to the machine’s parts catcher that helps remove swarf and coolant from each machined part.